Developing an electronics product from scratch is not an easy task. It’s more demanding than merely building an electronic component. The industrial design team should keep their eyes on every aspect for better risk mitigation prior to sending the design for prototyping and mass production. There’re some common electronic design mistakes that have been proven too costly for any designer and their companies to make.
Table of Contents
5 Fatal Electronic Design Mistakes
1. Not Optimized for Manufacturing
The biggest gap between hardware designers and electronics manufacturers is the manufacturers often find the designs not optimized for manufacturing. Design for manufacturing, also known as DFM, refers to the practices in electronics design that optimize the products for manufacturing. However, many hardware designers lack the industrial manufacturing experience and sometimes come up with ideas that aren’t feasible from the manufacturers’ perspectives. Therefore, sometimes manufacturers might have difficulty fabricating functional PCBs or getting the assembly done without any hiccup. Even if the manufacturers can, not implementing DFM often lead to increased costs and potential reliability issues.
In electronics manufacturing, the slightest mistake would have big impacts on the production schedule and resulting in extra costs. For instance, inexperienced designers might forget to include fiducial markers and tooling strips on the design of PCB, which would be destructive if the PCB is mounted with SMD components. Usually, fiducial markers are required to place fine-pitched SMD components accurately, and the tooling strips are necessary to secure the PCB on the machine.
If you’re working with a China electronics manufacturer, you should confirm whether your design is DFM friendly before starting the manufacturing process.
2. RF Design Mistakes
RF design is much more difficult to work with compared with its lower-frequency counterparts. The slightest mistakes can have great impacts if they’re not identified and solved at the beginning phrase. Impedance matching is critical to avoid signal reflection in RF circuits. The transmitted signal would suffer from degradation if the transceiver and the antenna have mismatched impedance.
Usually, RF circuits are developed to work with 50 Ohm impedance. Hence, you have to make sure that the components and traces are built with 50 Ohm in mind. The most challenging part is to keep the PCB trace at balanced impedance to the source and load. The impedance of PCB traces is affected by a variety of factors, including trace width, height, board thickness, PCB material, etc. Apart from impedance matching, you have to make sure the RF circuit is not causing EMI problems to circuits nearby. It’s essential to maintain a continuous ground place below the high-frequency RF trace to avoid a ground loop.
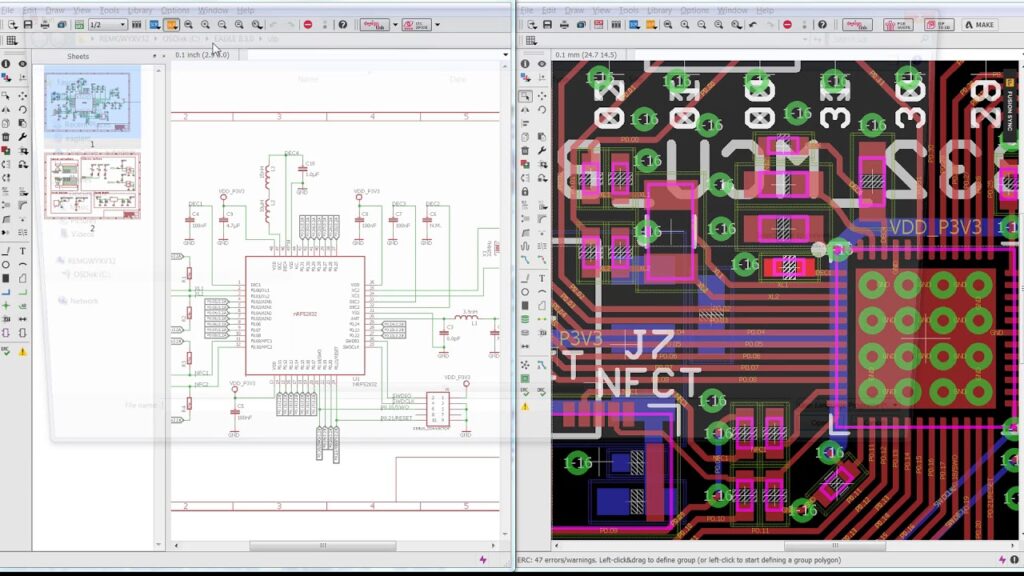
3. Wrong Cost Estimation
The most fatal reason for certain successful electronics crowdfunding campaigns failing to delivery the goods is wrong cost estimation. A browse through crowdfunding platforms like Indiegogo and Kickstarter you might come across reviews of angry backers who never received the goods from a successful campaign. The reason most probably is wrong cost estimation which put the product in a bottlenecked place. Building a functional electronics product is different from launching a profitable product into the market.
The key difference is getting a cost estimation done without too big a difference before the design starts. You wouldn’t want to wait till the fabrication of the PCB to start calculating the costs for reach component, assembly, packaging, etc. People often presume that there’s a discount when you’re buying in bulk, it is in most circumstances. However, some components are quite costly, even if you’re buying in large quantity, the price difference is small. Ultimately, it’s not practical to proceed with a design if its costs exceed the estimated sales price. Therefore, it’s critical to get a reliable cost estimate before starting the design.
4. Product Enclosure Mistakes
If your electronics products involve any enclosure, you must make sure it’s DFM friendly. It’s easy to print a 3D enclosure prototype within a short time with 3D printers. However, it’s not easy to reproduce a 3D prototype in volume, and you would have to opt for injection molding for mass production. With injection molding, first you have to build the mold for the enclosure, then it’s used to mass-produce the plastic parts. In general, injection molding has more restrictions on the shapes. The more complex the shape is, the high the costs you would have to pay. Sometimes you might not get the desired results. It’s best to verify the enclosure prototype with the electronics manufacturer.
5. Complicated PCB, Limited Budget
Electronic products are getting smaller and thinner than ever before, which means squeezing tinier components into a compact PCB from the electronic designers’ perspectives. As a result, PCB spaces become a luxury, and designers are forced to use advanced routing strategies to make the best out of limited space. Two of the most used strategies are blind or buried vias on a multilayer PCB. The former connects two middle layers while the latter connects an outer and a middle layer. Both are quite challenging to manufacture and result in extra costs.
If you’re designing a flex or rigid-flex PCB, you have to understand the best practices for the manufacturing process. For example, avoid sharp corners on traces along the bend, do not place vias and pads on the bending area, use teardrops to strengthen trace-to-pad joints, etc. Failing to comply with the best manufacturing practices will make the production process difficult and costly.
Leave a Reply