If you’ve ever wondered how phones are made, the 2019 China mobile phone manufacturing technology exhibition held in Dongguan recently is the perfect opportunity to experience the process from start to finish and learn how phones are made. Like visiting Chinese factories, the greatest perks of participating in trade fairs is, I always find myself continuously learning, absorbing and soaking up the expertise, latest trends and vibrant atmosphere of the industry.
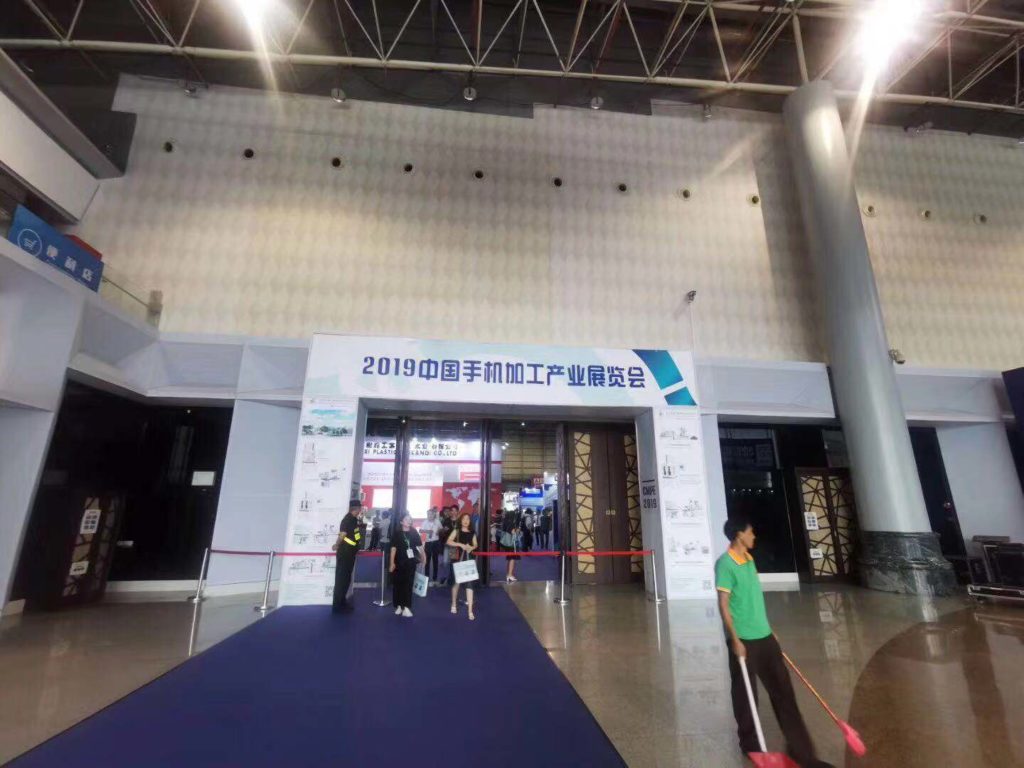
Indisputably known as Factory of the World, China is home to the manufacturing of top 5 smart phone brands, while the southern city of Dongguan, a key-player in the forefront of mobile phone manufacturing, houses the manufacturing bases of leading domestic smart phones in China, including Huawei, OPPO, VIVO, Jinli and many more. In 2017, the total shipments of smart phones from Dongguan reached 356 million pieces, taking up 20% of the world’s total shipments. Its leading position accounts for the reason why it’s chosen as a prime location to hold China mobile manufacturing fair.
In the early morning on the 29th September, 2019, we headed over to Guangdong Modern International Exhibition Center in Dongguan, where the epic electronic manufacturing show was in full swing. The visiting in the early morning usually means avoiding the crowds in the afternoon when it gets busy. The exhibition is well organized into four exhibition areas: 2.5D and 3D glass, mobile phone precision ceramics, plastic casing and wireless charging. A detour navigating through the massive complex with an eclectic range of products in display and bantering with the exhibitors, it gives us a deeper appreciation of how everybody’s daily essential is brought into life.
Materials
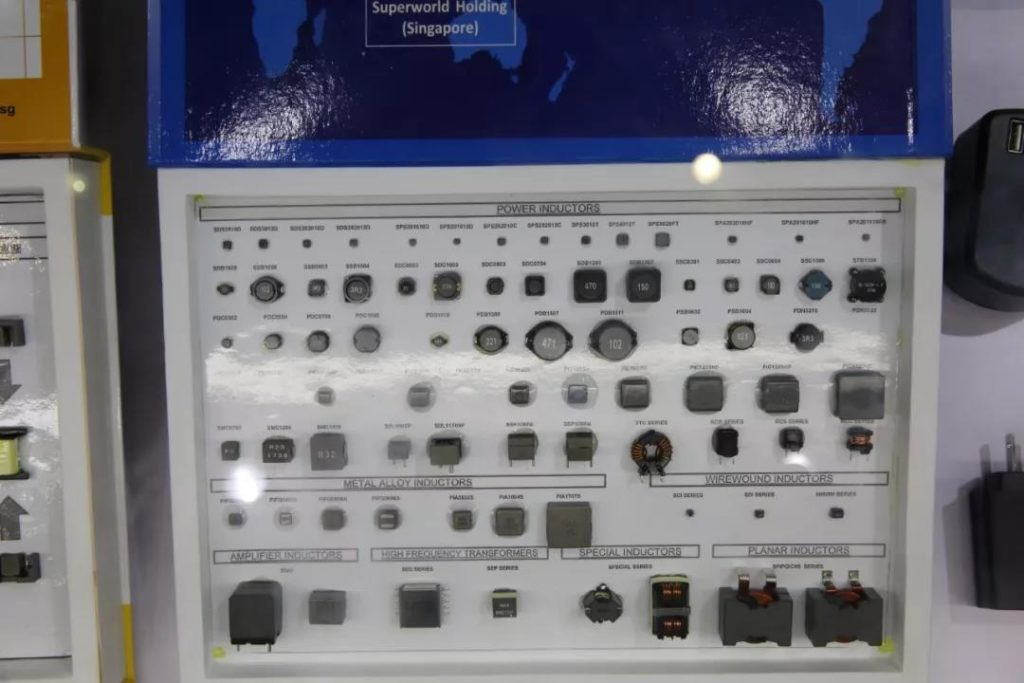
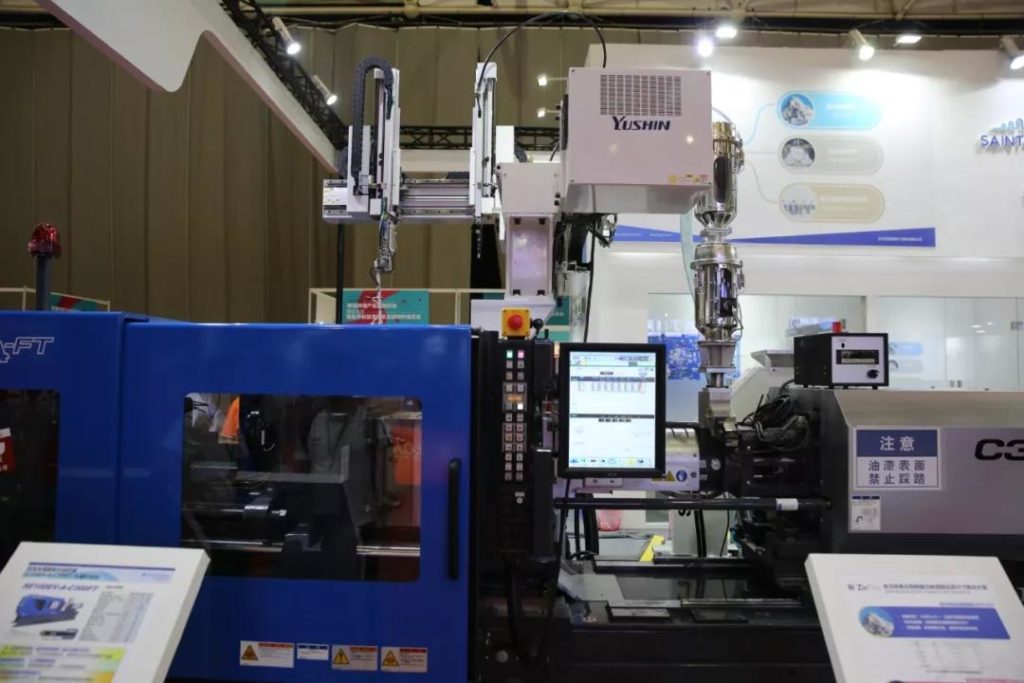
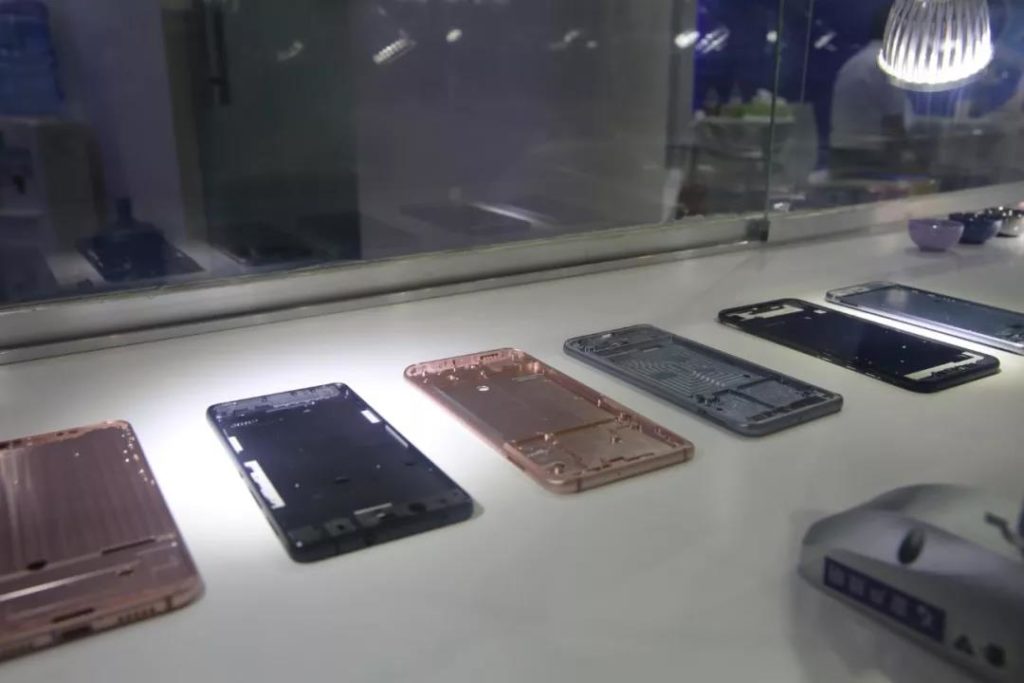
What mobile components to smart phones is what soil and water to plants. A smoothly running and functioning mobile phone relies largely on the hundreds of components that back it up.
SMT
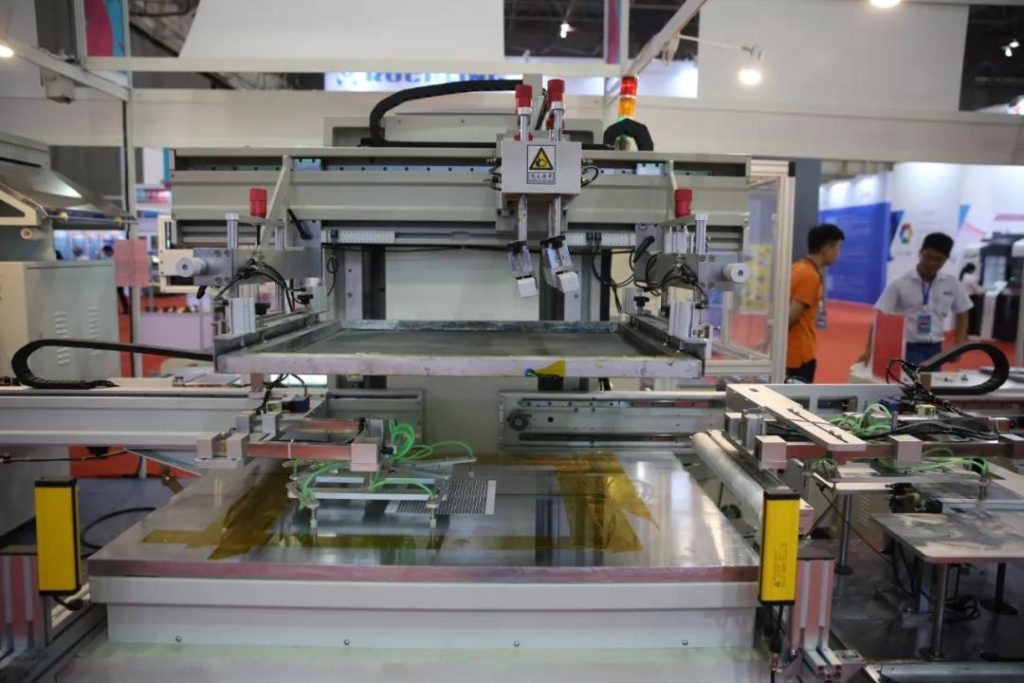
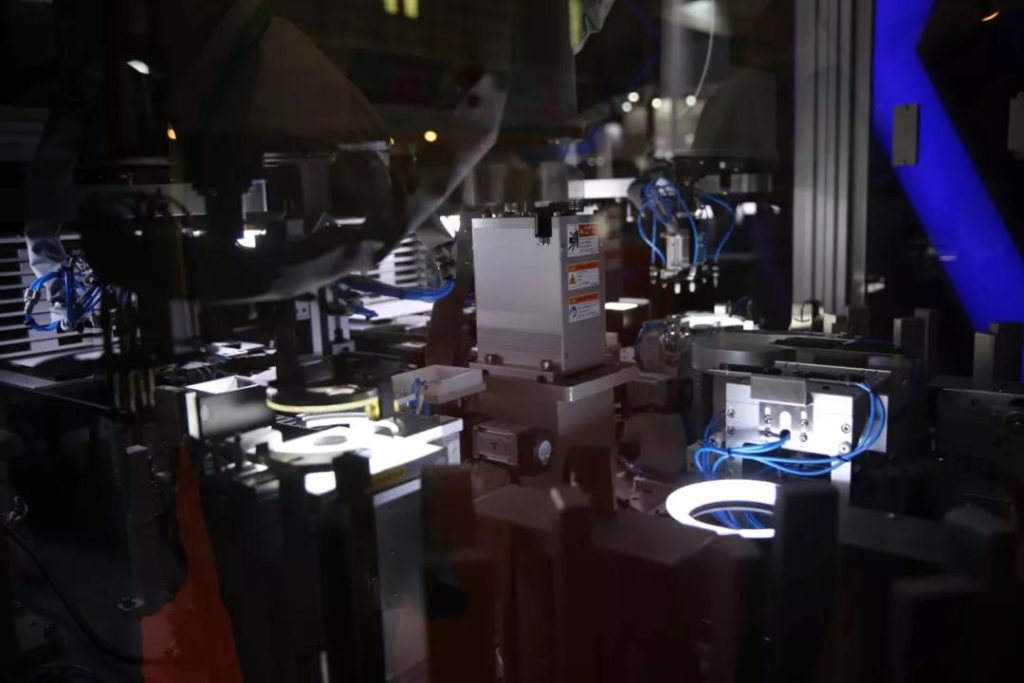
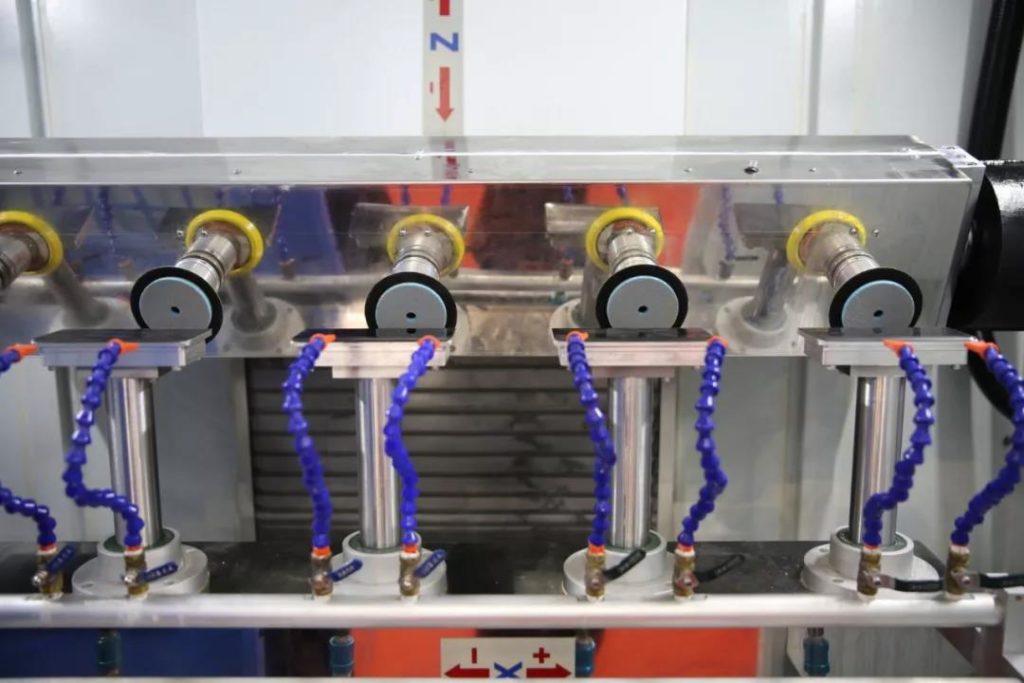
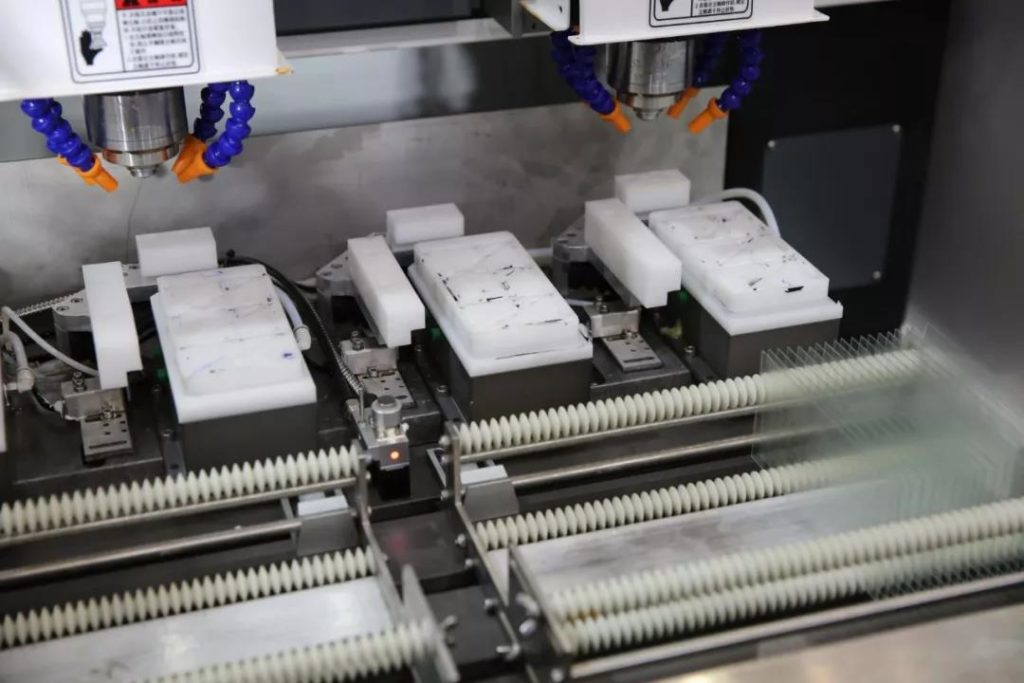
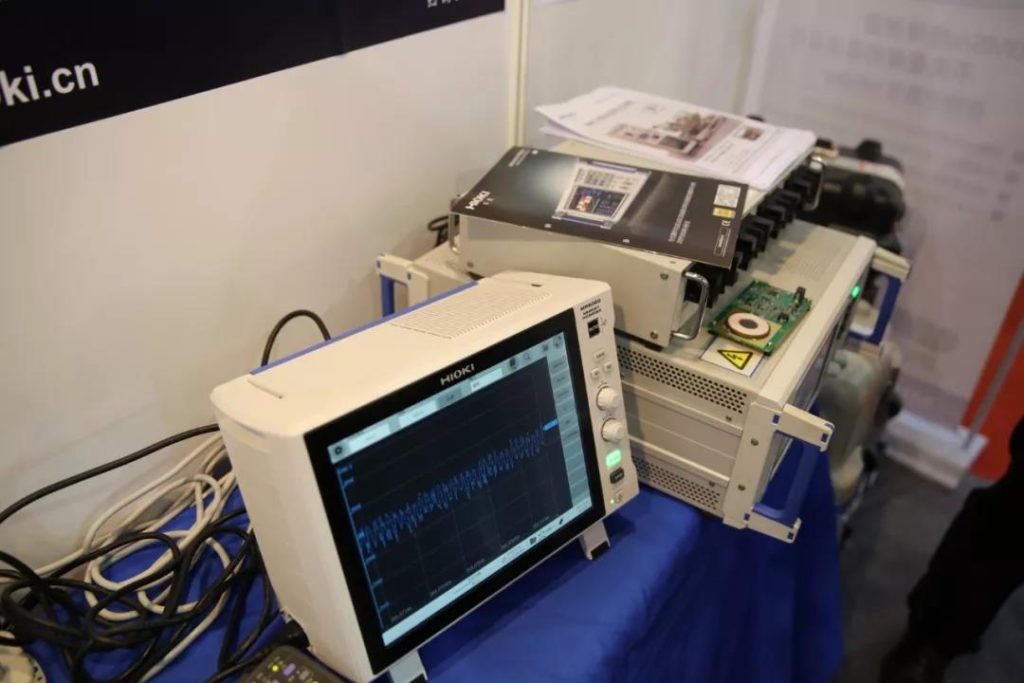
Short for surface mounted technology, SMT is a major process of the mobile phone manufacturing process involving three parts: printing circuit, chip mounting, and temperature return. As we’ve previously wrote from a visit to Huawei factory in Dongguan (Visiting Huawei Factory: How a Phone is Made in 28.5 Seconds) most of the assembly lines are highly automated requiring only one or two operators on site. Besides, a series of stringent robot tests and manual tests are also carried out to ensure things go on the right track. What’s shocking is that quality inspection part tends to be more manually involved than the highly automotive assembly lines.
Assemble
Later, all the tiny mobile parts including speaker, camera, earpiece, button, screen and many more are assembled together using various equipment.
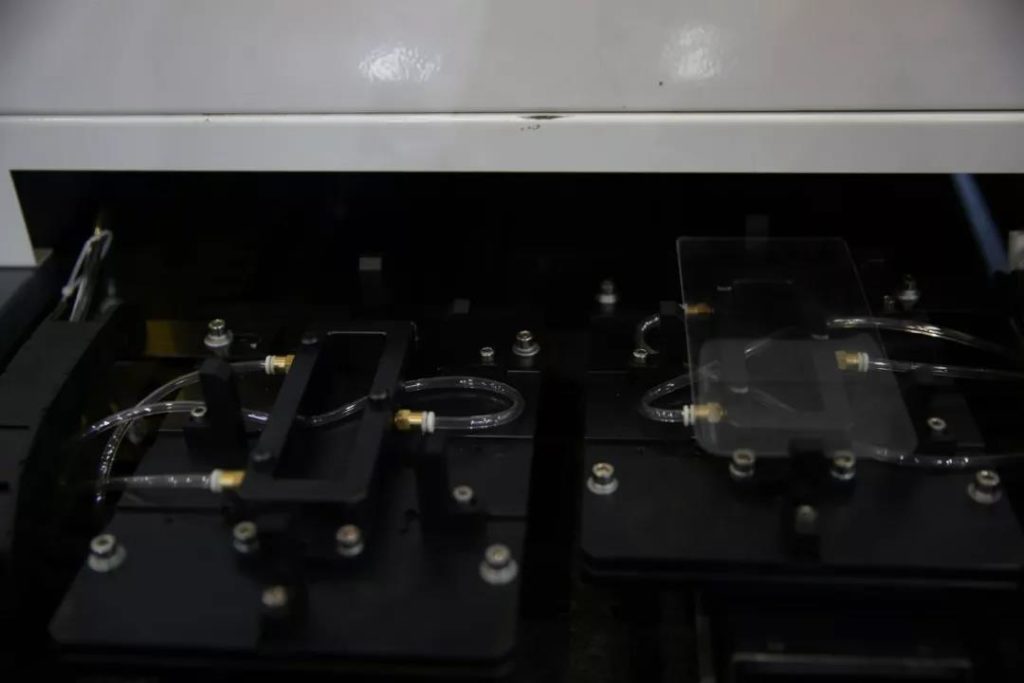
Machine to inspect the screen size of the mobile phone
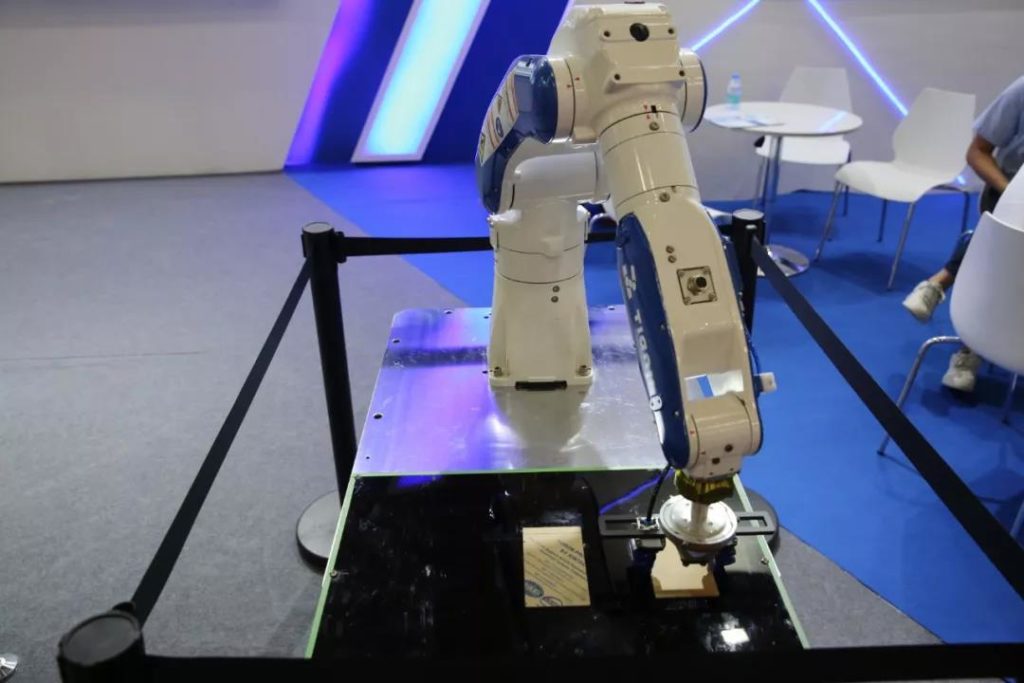
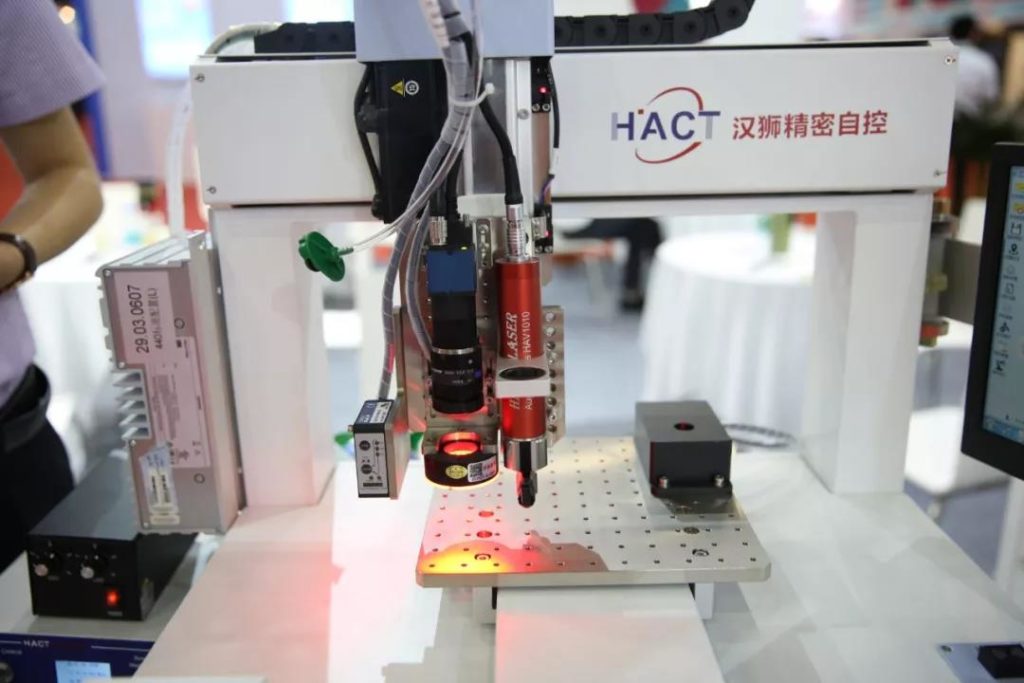
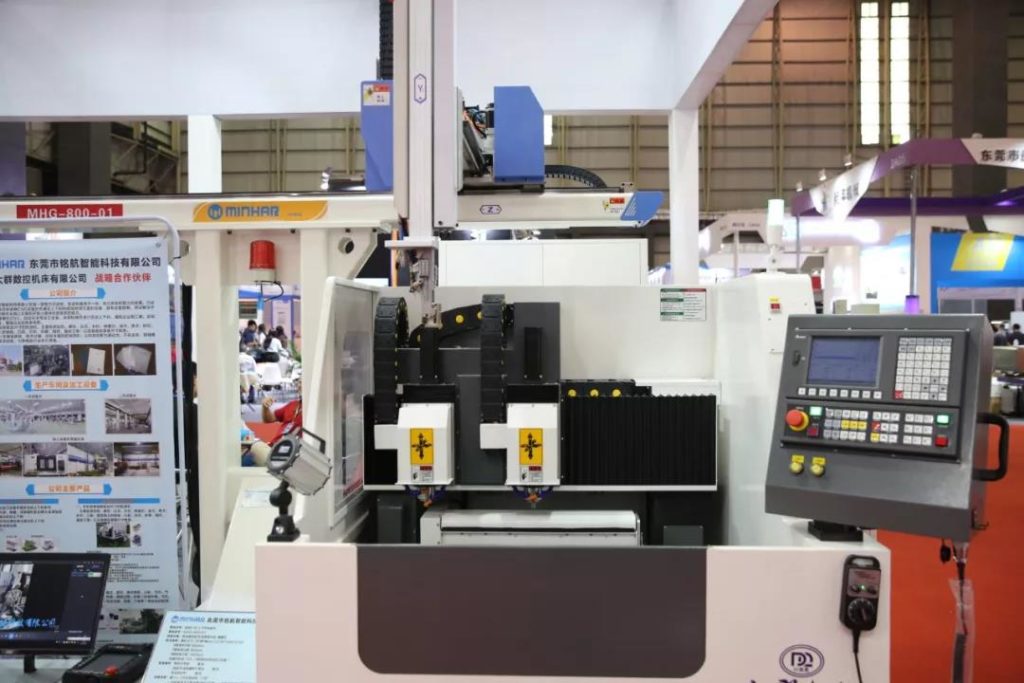
Automatic assembling machines
Inspection
Quality inspection usually involved two parts: visual inspection and MMI engineering test.
Visual inspection: check whether there’re any scratches, cracks, missing parts, broken screen, color difference, etc.
MMI engineering test: functioning tests more leaning towards the performance of speakers, earpieces, microphones, LCDs, cameras, buttons, touch screens, etc.
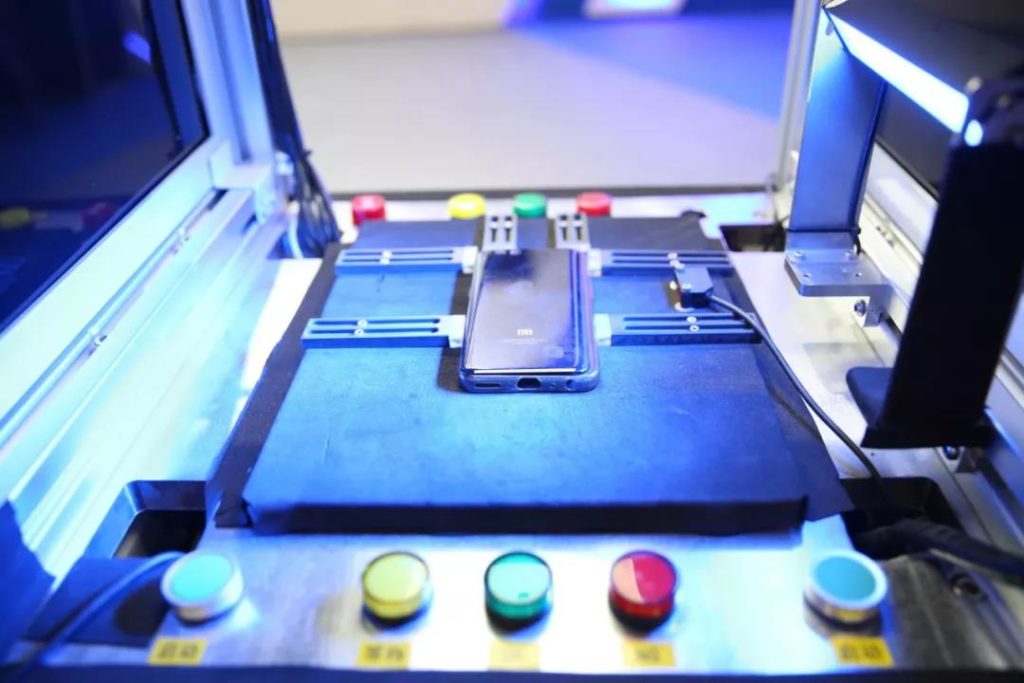
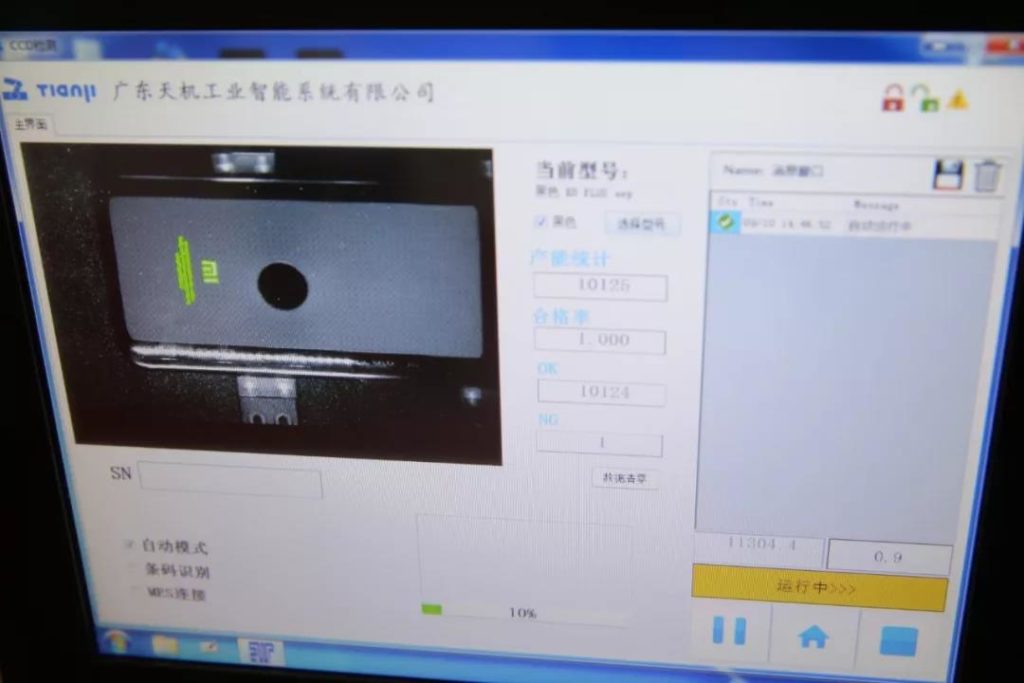
Logo inspection
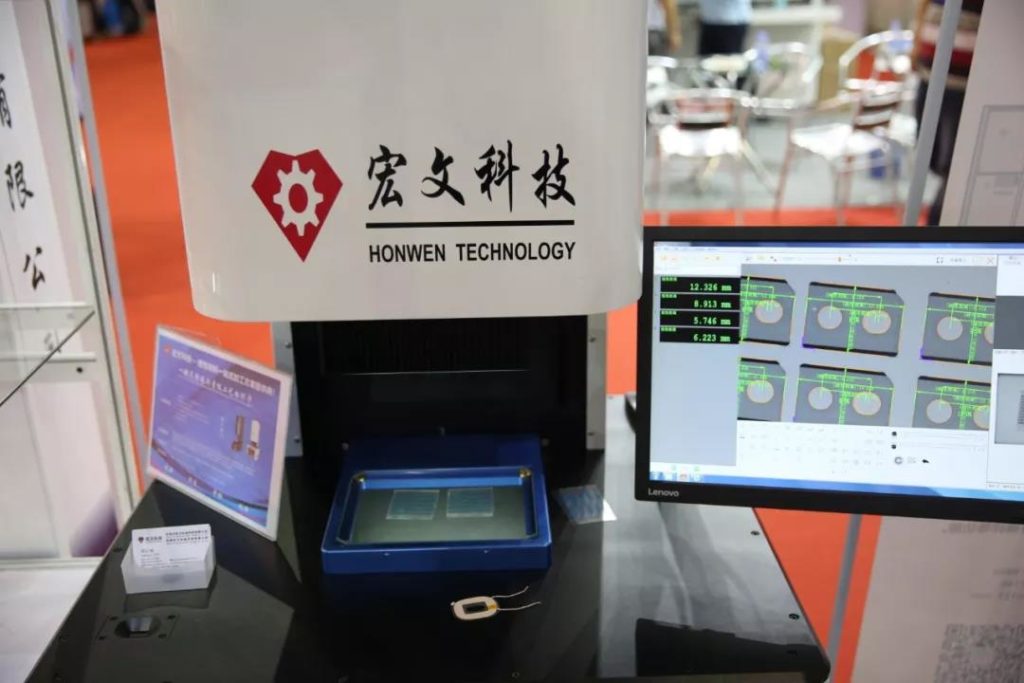
Testing of other tiny components
What’s shocking is that before launching into the market all the smart phones have to go through another round of stringent tests. For example, it will be dropped 150 times from 1 meter high, the front, back and side of the phone will also go through an anti-drop test of 42,000 times, the buttons on the side will also be clicked 200,000 times by a 1kg force, the screen being clicked 100,000 times. It has to go through high temperature, rain, salt, dust, distortion, violent plugging and unplugging to finally become the essential gadget in your hands.
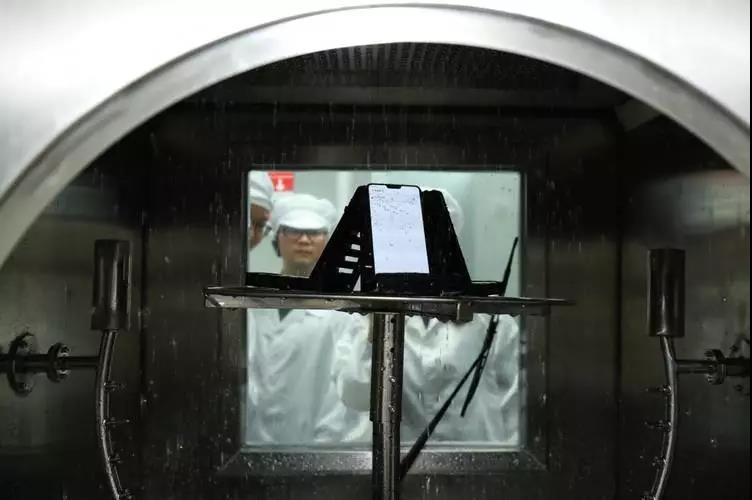
Apart from participating in the fair, the place comes alive with a series of seminars held every days, where leading mobile phone manufacturers, mobile spare parts manufacturers, intelligent application service providers and other companies involved in the industry share the expertise and latest trends in mobile phone manufacturing.
sir i want sam mobile parts & assresz soo i want your contct & email.id
iam froom pakistan
Kindly contact us via WhatsApp +86 1821849438, thanks.