Last week I was invited to visit a USB cable manufacturer in China, together with my classmate from junior middle school. My classmate, Awen, now boss of a multi-million dollar tech company, started humbly working in a Huaqiangbei shop dedicated to wholesale mobile phone charging cables, and the factory we visited was their previous supplier. 🙂 Feeling shocked? Aren’t shops in Huaqiangbei representatives of factories? The truth is, probably 80-90% of shops in Huaqiangbei electronic markets don’t own any factories, and they’re just wholesalers. Anyway, most of them are able to offer you better prices and stocks with long years of partnership with the factory than buying directly from the factory as a new customer unless you order a lot.
If you’re looking to buy wholesale USB cables from China and wonder how they’re manufactured, this post will walk you through the manufacturing facility, and reveal the process of USB cable manufacturing.
Charging cable consists of several parts, including two connecting ends, the conducting wires inside that are wrapped by a cover.
The same with most electronic components, the wires inside are made from silver or copper as these materials work perfectly as conductors. Meanwhile, the connectors on both ends of the cable are often made from copper-zinc alloy, also known as brass. Most of them are usually coated with another layer of gold or nickel. To help better differentiate both ends, the connectors are designed in various shapes. Besides, they come in different types to maintain compatibility with new devices, i.e., type-A (used in devices like desktops, media players and gaming consoles), type-B (used in smartphones, printers and hard drives), type-C (the latest incorporated in Apple’s 12-inch Macbook), mini and micro USB, and the lightning (the connector to Apple’s recent devices).
Inside the China cable factory, different apartments are working continuously. First, unprocessed raw cables that are outsourced from downstream suppliers are cut in 1mm or 2 mm to meet different requirements of customers. Then, the wires at both ends of the cables are exposed and connected to terminals via tin soldering. Next step, injection mould machines are used to ensure overall covering and ultimate electrical performance. Electrical tests are conducted many times to double confirm the electrical performance, besides, the overall appearance are also meticulously inspected to avoid any flaws. Then it comes to the final step of packing.
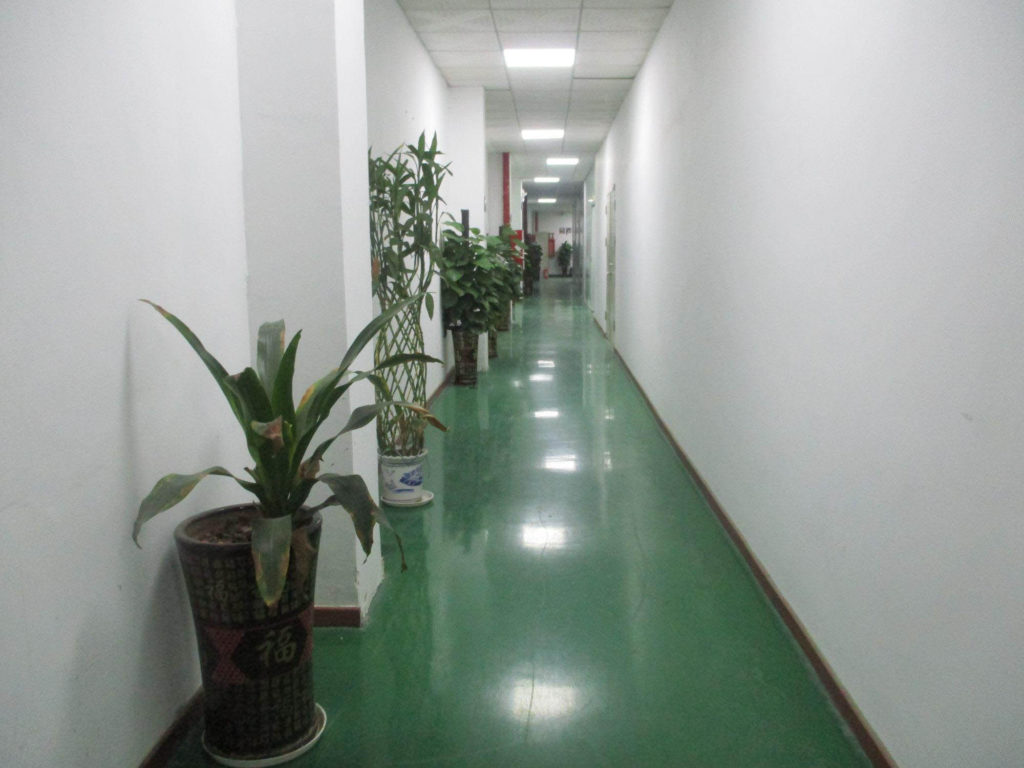
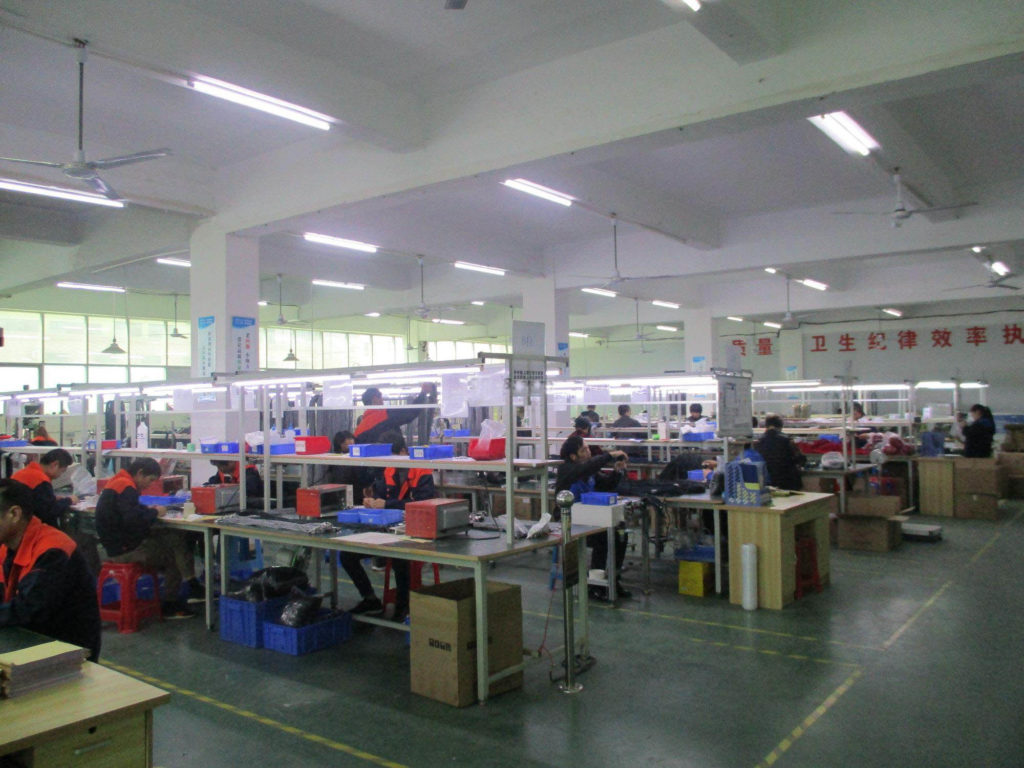
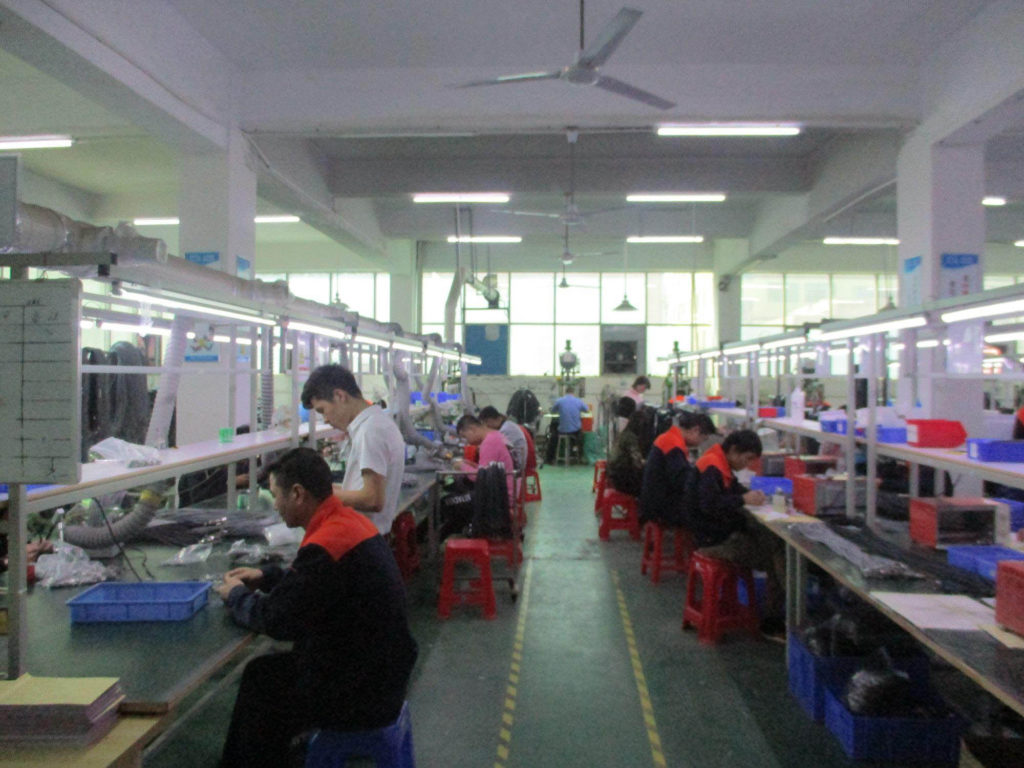
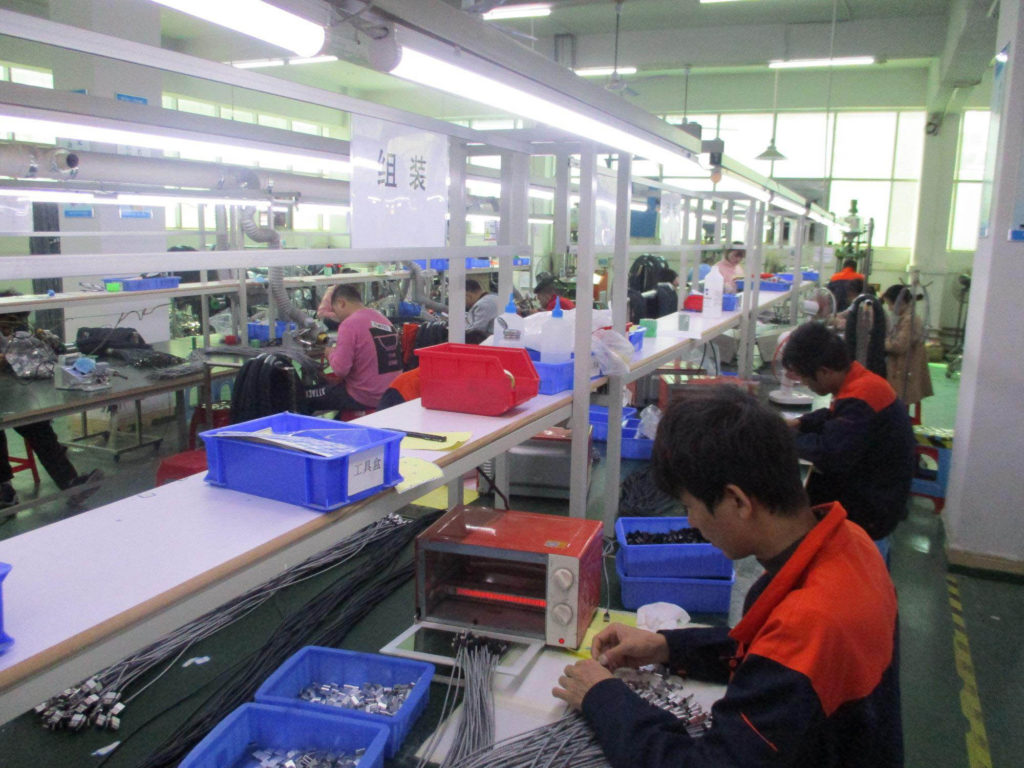

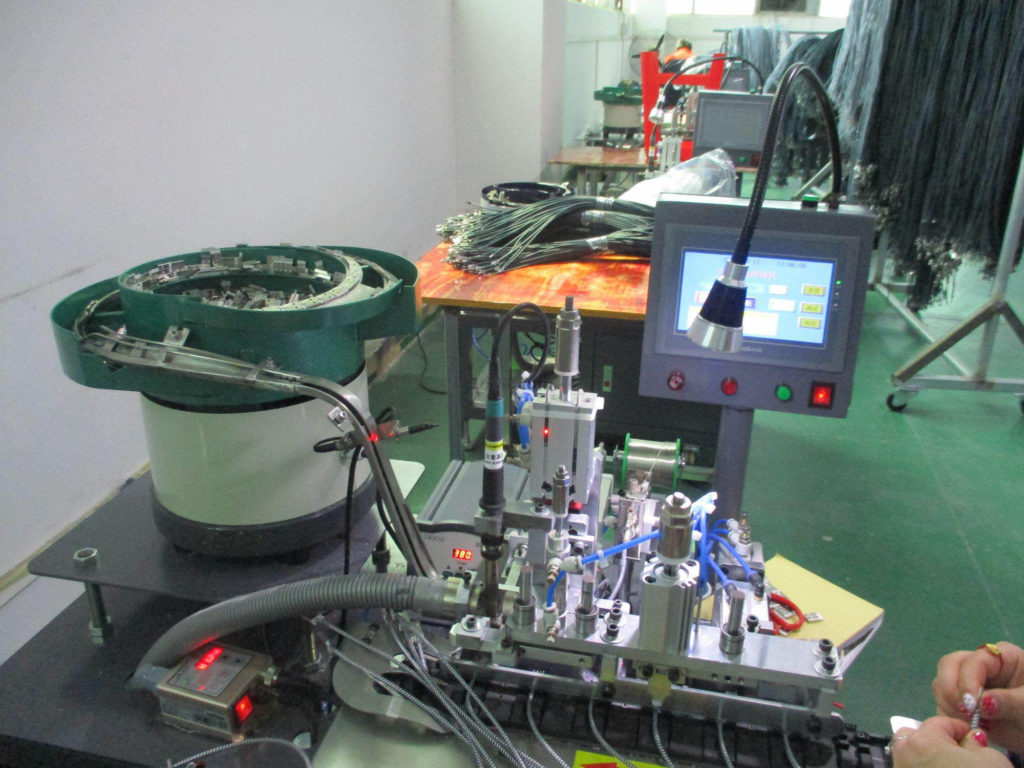
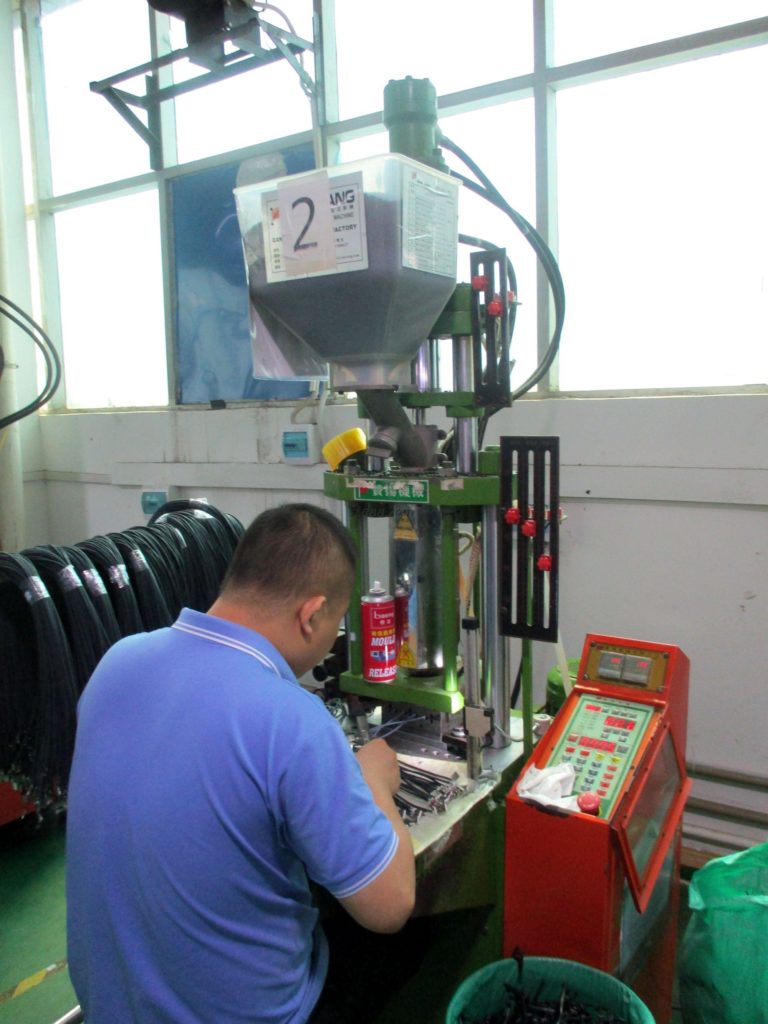
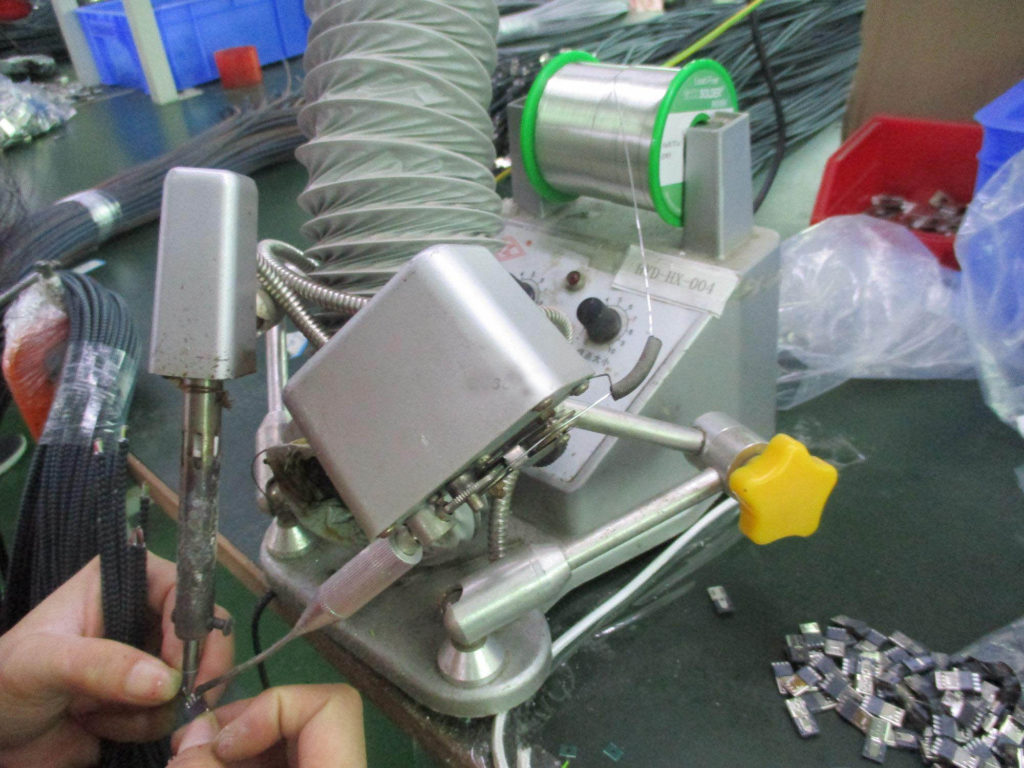
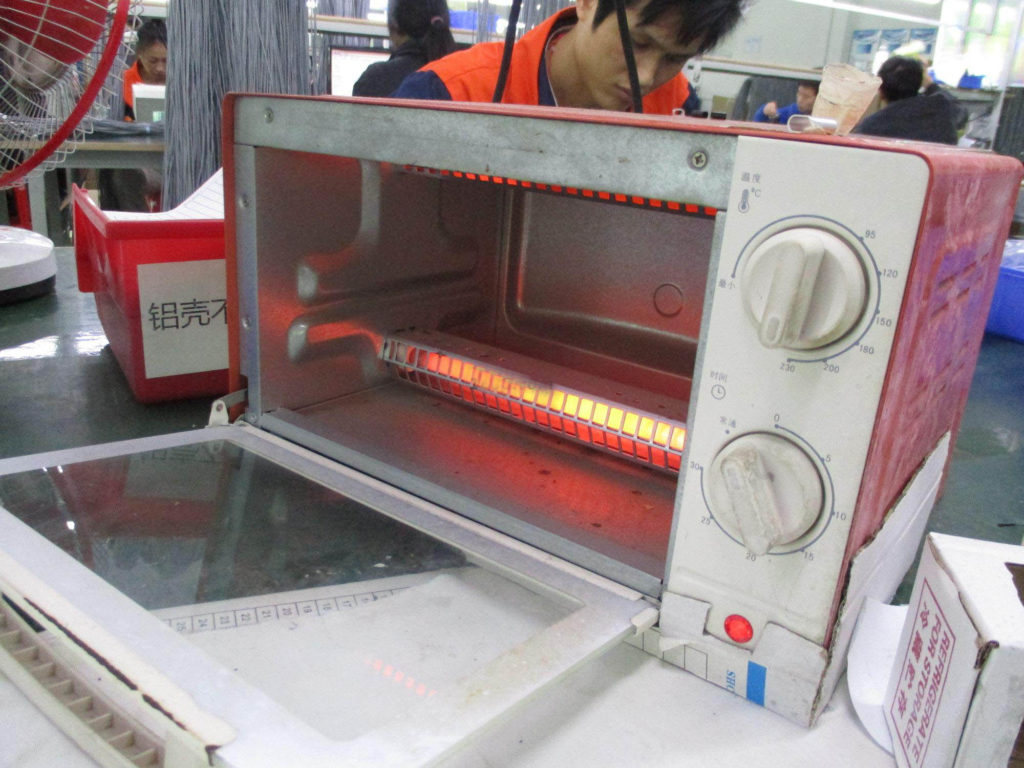
Hi d I hope all ok ; I want big Quantity
Hi, thanks for reaching out. Please send us enquires via WhatsApp/wechat: +86 182 1849 4138 what kind of electronics you want to buy, thanks.